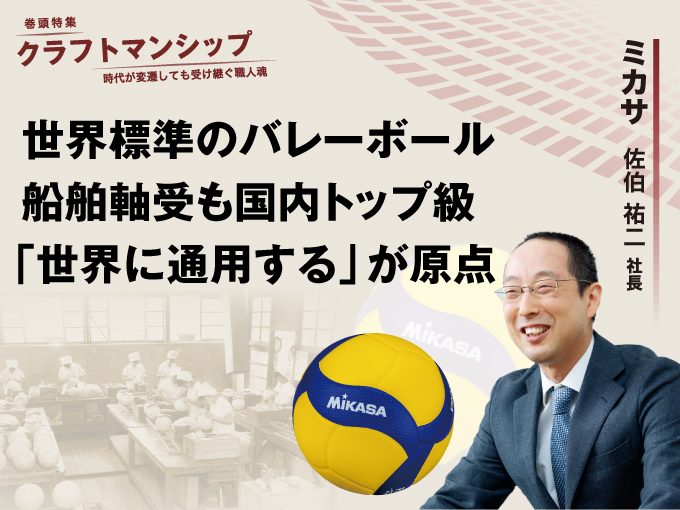
日本の製造業が岐路に立たされている。中国などの台頭を受け、お家芸といわれた液晶ディスプレーや半導体、家電などの世界シェアが低下。政府は半導体分野に狙いを定め、国内生産の強化に巨額の補助を決めた。
広島の基幹産業「自動車業界」も世界的な環境規制の加速や電動化の荒波に巻き込まれる。全ての分野で人手不足を解消する省力化・自動化やDXへの対応を迫られており、メーカーだけでなく、部品などを供給する中小企業の変革が欠かせない。これまで日本のものづくりは基幹技術を磨き、時代に合わせて世界に名だたる製品を生み出してきた。いま再び、職人魂が問われている。
ロータリーエンジン(RE)を電動化に応用したマツダ、手焼きの卵焼きを工業化し国内トップクラスに成長したあじかん、ゴム草履作りからバレーボール製造で世界一となったミカサの3社の事例から読み解く。
1991年にル・マン24時間レースで日本車として初優勝した「787B」は昨年、日本自動車殿堂「歴史遺産車」に選定。RE搭載車では67年発売の「コスモスポーツ」に続く。今年2月1日、36人の技術者が集まり「RE開発グループ」を復活させた。発電用などで一層改良するほか、環境規制が強まる中でカーボンニュートラル(CN)燃料対応など研究開発を進める方針だ。 1974年の本誌インタビューで当時の松田耕平社長は排出ガス規制の強化に触れ、「まず、いかにして現在の燃料でエネルギー効率を高めるか。長期的に見るとREの燃料はガソリンからアルコール系へ、そして水素へと進みそうだ」と話した。50年たった現在、同社は水素燃料のRE搭載車を世界で初めて実用化(2006年にリース販売)。CN燃料を使うロードスター(2・0L直列4気筒自然吸気エンジン)をスーパー耐久レースで走らせている。ものづくり企業にとって基幹技術を磨くことは無論、その時代に求められる形を模索し続ける姿勢が必要なのだろう。
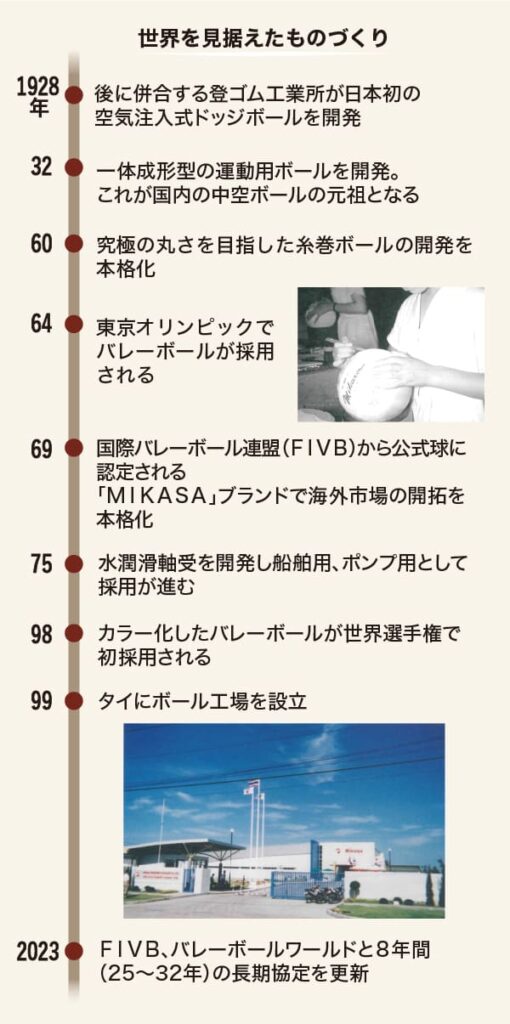
バレーボールの世界トップメーカーとして高い知名度を誇るミカサ(安佐北区安佐町)。実は同社はこれら競技用ボール以外にも国内でトップシェアを誇る製品がある。船のプロペラ軸を支える「軸受」だ。主流の油潤滑式ではなく、環境負荷の少ない水潤滑式で差別化を実現する。ボールと軸受(工業用品)の両事業は、ゴム加工という点で共通するが、業種は全く異なる。それぞれの業界で、トップクラスの製品をいかにして生み出したのか。そこには受け継がれる「世界に通用する商品を造る」という強い志があった。佐伯祐二社長は「中興の祖である3代目社長・仲田国市が海外市場を切り開いた。飽くなき技術力の追求と、世界を股にかけた血のにじむ営業活動の両輪があってこそ、今のミカサがある」と話す。ー初の空気注入式ボール開発同社の歴史は1903年にさかのぼる。ハワイに渡った創業者の増田増太郎氏が現地でゴムの可能性を感じ、帰国後にゴム草履などのゴム製品製造で創業。その後、手袋や自動車用のゴム製品、スポンジ製品など多品種に手を広げる中、開発を進めていたのがゴムボールだった。前身の広島ゴムを設立した1917年頃にはボールづくりを本格化し、試行錯誤の末、28年には日本初の空気注入式ドッジボールを開発した。ボール事業は戦後の46年に大きな転機を迎える。GHQ(連合国軍総司令部)が小学校体育にドッジボールを使えるように通達を発したことで需要が急伸し、全国の小学校に供給。最盛期は年間約20万個を製造した。50年からバレーボールの製造を始め、64年には東京五輪に採用された。しかし実際は同業8社と共同して造っており、ボールにミカサの印字はなかった。「他社に負けない強みが必要だ」と考えた仲田氏はこのバレーボールに注目して海外に渡り、69年に国際バレーボール連盟の公式球の認定を獲得。それ以来、世界の大舞台で使われ続ける。ー球体の難しさボールには球体という形状の難しさに加え、思い通りのプレーを実現する操作性、耐久性などが求められる。同社はそのニーズを常に現場に求めた。国内強化合宿などでトップ選手らにヒアリングを行い、使い心地を調査。そうして、変形しやすいゴムを丸く保持する技術、空気穴のバルブがある側との重量バランス、汗がついても滑りにくい表面のくぼみ、テレビに映えるカラー化など、限りない試行錯誤を繰り返してきた。世界に通用するものづくりへの姿勢が、同社の技術革新の軌跡と重なる。
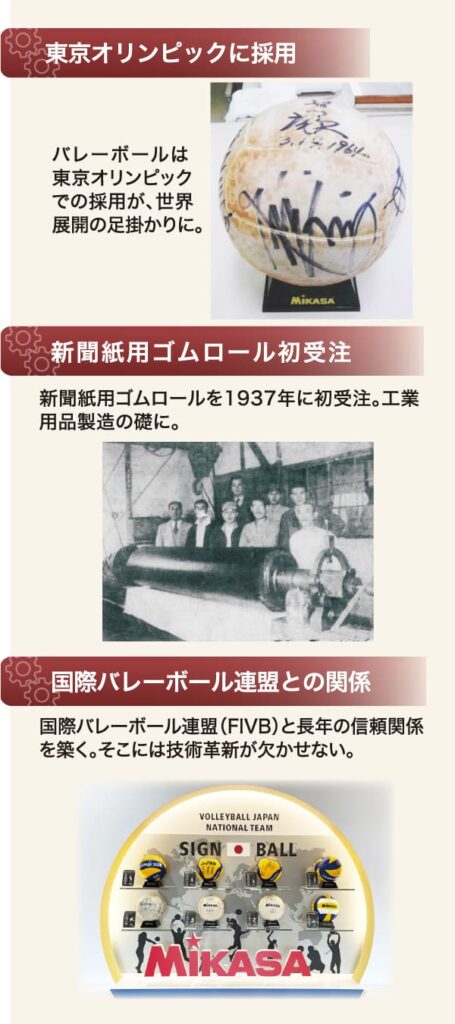
仲田氏は1979年の新聞インタビューで「わが社は国内で戦う会社ではない。世界の中で生きていかなければならないので、一生懸命努力する姿勢は変わらない」と言い切る。佐伯社長は「ボールは現在、タイ工場で製造しており、表皮を貼る作業は今でも一つずつ手作業だ。表皮はそれぞれわずかな違いがあり、現物合わせが必須。良いものを造るという職人としてのこだわりがここにある」と話す。ー環境に優しい軸受で海外へもう一つの事業の柱である、軸受をはじめとする工業製品の振り出しは、1937年に初受注した新聞紙用ゴムロールだ。戦後の高度経済成長の流れに乗り、工業用のゴム製品を伸長。一時はマツダ向けのゴム製品も手掛けていたが、「世界で一番を目指すなら自社で全部やろう」と、仲田氏が下請けを辞めたという。工業製品部門の主力である「FFベアリング」は、船舶や大型ポンプのプロペラ軸を支える部品だ。ゴムと特殊な樹脂加工で摩擦抵抗を大幅に減らし、低燃費と長寿命化を実現する。主流の油潤滑式は油漏れによる海洋汚染が懸念されており、水潤滑式の同社製品に追い風が吹く。これまでの実績を基に、海外市場の開拓に向けロビー活動を進めている。ー挑戦を恐れない組織づくり佐伯社長は自社のものづくりの文化についてこう語る。「当社には挑戦の機運がある。未知に挑むフロンティア精神が基盤となって、ものづくりへのこだわりにつながっている。2014年に私が社長になってから、改めて『失敗してもいいから、挑戦しよう』と社員に幾度となく伝えている。世の中は常に動いており、変化に対応し続けるほかない」。2年前に従来の開発部門と別に商品企画チームを設け、市場ニーズに応じた開発を一層強化する方針を掲げる。今後の課題はブランディング、マーケティングと断言する。「ボール事業は、世界の巨大資本が競合先だ。良いものを造るだけでは今のポジションを維持できない。造って終わりではなく、ファンになってもらう仕掛けが必要だ。軸受も海外市場の開拓に本格的に乗り出している。成長余地は大きく、これからが勝負だ」。
この記事が気に入ったら
フォローしよう
最新情報をお届けします